Navigating medical device guidelines can seem daunting for buyers. From certification requirements to industry-specific standards, understanding what to look for ensures safety and compliance. Whether you are sourcing surgical tools or first-aid kits, knowing the essential steps saves time, money, and potential liability.
Key Points to Remember
- Always verify certifications from recognized organizations.
- Check for FDA or CE marks where applicable.
- Understand industry-specific requirements for different devices.
- Look for a clear traceability record in manufacturing.
- Research the supplier’s history for reliability and compliance.
Why Certification Matters
Certifications ensure that the device meets established safety and performance criteria. Recognized marks like FDA approval in the United States or CE markings in Europe signify adherence to stringent health and safety requirements. For instance, an FDA-certified surgical tool guarantees sterility and accuracy, critical for patient outcomes.
Industries like healthcare, emergency response, and personal wellness demand unique certifications. First-aid kits, for example, must comply with OSHA standards in workplace settings. When you purchase devices, confirm they meet the necessary local and international regulations.
Steps to Evaluate Suppliers
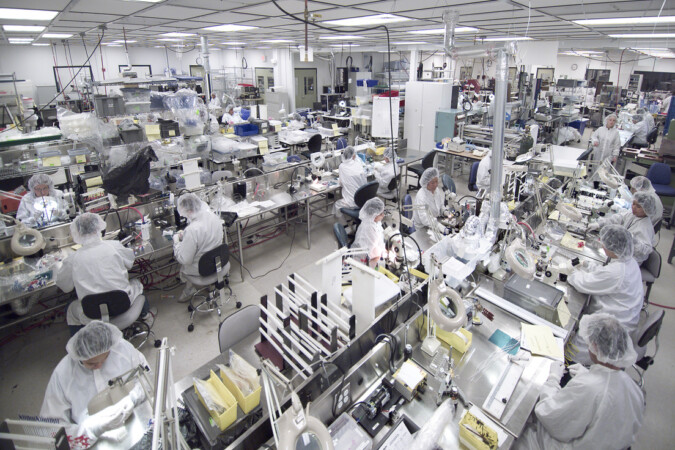
Buying from reputable manufacturers reduces risks. Poor-quality devices can cause harm or fail during critical moments. To ensure reliability:
1. Research the Supplier
Look into the company’s history, reviews, and product recalls. Reliable manufacturers like Yeyetac design kits based on field feedback, ensuring functionality in emergencies. Their tactical medical kits cater to real-world needs, making them a trusted option.
2. Check Certifications
Always ask for proof of compliance with standards like ISO 13485 for quality management. This certification guarantees the manufacturer follows rigorous processes to ensure device quality and reliability.
3. Request Documentation
Ask for a Declaration of Conformity (DoC) or equivalent documentation. This outlines the standards the device meets, offering transparency into its compliance.
4. Inspect Traceability Records
Reliable suppliers keep a traceable record of their materials, manufacturing processes, and inspections. This ensures accountability at every step.
Common Requirements by Industry
Different industries enforce varied requirements for medical devices. Below are some examples:
1. Healthcare Sector
Hospitals demand devices with precise sterility and durability standards. Devices like surgical gloves must pass biocompatibility tests to avoid reactions during use.
2. Workplace Settings
Workplace first-aid kits must meet OSHA guidelines. Contents should include bandages, antiseptics, and tools compliant with health safety protocols.
3. Emergency Services
For EMTs, devices such as tourniquets and wound dressings require rigorous testing for rapid deployment during emergencies. Organizations like NAEMT recommend devices tested in real-world conditions.
4. Personal Use Devices
Wearable devices, like blood pressure monitors, often need FDA clearance. Consumers should ensure the devices offer accurate measurements and are user-friendly.
Recognizing Quality Certifications
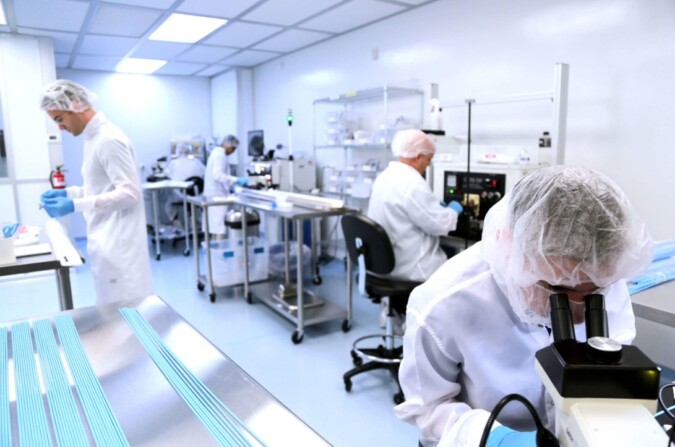
Certifications help buyers distinguish between compliant and subpar products. Below are common certifications and their meanings:
- FDA (U.S.) ─ Covers safety, efficacy, and marketing of devices.
- CE Marking (Europe) ─ Ensures compliance with EU directives.
- ISO 13485 ─ Focuses on consistent device quality management.
- OSHA Approval ─ Ensures workplace kits meet safety standards.
Challenges with Non-Compliant Devices
Purchasing uncertified devices creates risks. Substandard materials can lead to malfunctions, harming users or violating legal guidelines. For example, counterfeit surgical gloves lacking sterility can cause infections in patients.
A recent case involved unregulated pulse oximeters that provided inaccurate readings. This jeopardized patient care, underscoring the importance of choosing certified products.
Practical Tips for Buyers
Know Your Standards
Research local requirements before purchase. OSHA compliance is necessary for workplace kits, while CE marking is vital in Europe.
Stay Updated
Guidelines often change. Ensure devices align with the latest standards by checking updates from regulatory bodies.
Test Samples
Before bulk purchasing, request product samples to verify functionality. Simple checks, like using a pulse oximeter on multiple individuals, confirm accuracy.
Verify Supply Chain Practices
Ethical sourcing and quality controls ensure reliability. Ask the supplier about their inspection processes and raw material sources.
Numbers Tell the Story
Below is a breakdown of common certifications by type and their applications:
Certification | Application | Key Benefit |
FDA | U.S. market devices | Ensures safety and efficacy |
CE Marking | European market devices | Demonstrates EU compliance |
ISO 13485 | All manufacturing processes | Quality assurance globally |
OSHA | Workplace first-aid kits | Workplace safety compliance |
According to a Deloitte report, companies using ISO-certified suppliers reported a 25% decrease in product defects.
What to Do Before Purchasing
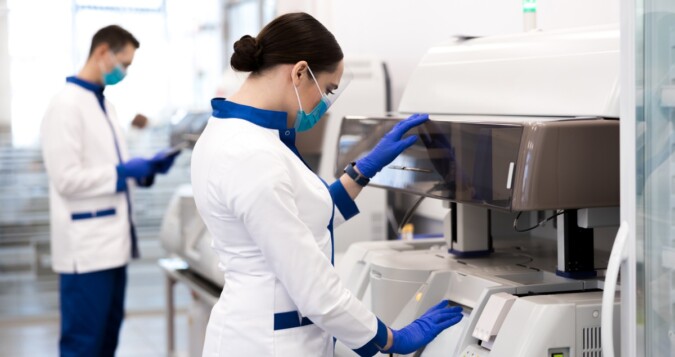
Ask manufacturers questions to avoid surprises:
- Can you provide certification proof?
- Do your devices meet local and international guidelines?
- What steps are taken to ensure quality control?
- Have any product recalls occurred recently?
Frequently Asked Questions
1. How do I verify if a device meets guidelines?
Check for certification marks like FDA or CE and request supporting documentation.
2. Can a product be used without approval?
Using uncertified devices risks legal penalties and potential harm, depending on your location.
3. How often should workplace kits be updated?
Review OSHA guidelines annually to ensure compliance with changing standards.
4. What if a manufacturer refuses to share documentation?
Avoid suppliers unwilling to provide transparency. Seek alternatives with a reliable reputation.
5. Are all first-aid kits considered compliant?
Not always. Kits should include essential items and meet industry-specific requirements for certification.
6. What are the consequences of using non-compliant devices in the workplace?
Using non-compliant devices may lead to safety hazards, legal issues, fines, and potential injury to employees, as well as damage to your organization’s reputation.
7. How can I ensure the quality of first-aid kit supplies?
Verify that items in the kit are from reputable manufacturers, have not expired, and meet relevant safety standards or certifications for your industry.
Conclusion
For buyers, choosing safe and compliant devices involves more than cost considerations. Certifications, supplier reliability, and adherence to industry requirements ensure quality and safety. Trustworthy manufacturers, prioritize safety through continuous innovation and feedback.
By asking the right questions and verifying certifications, you can confidently invest in devices that meet rigorous standards.